Distillery Planning And Equipment Considerations
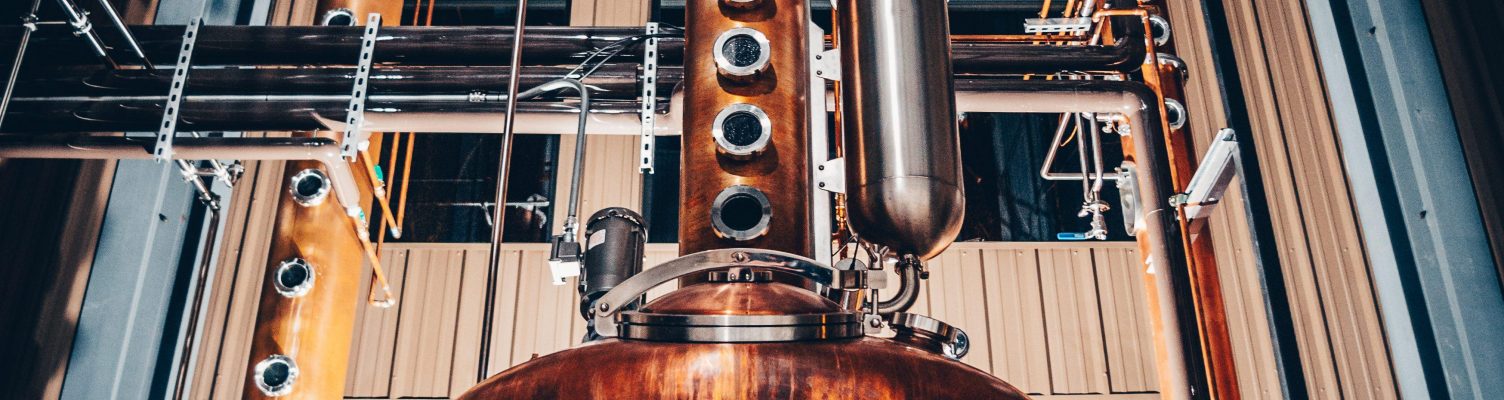
November 25, 2019
WHAT EQUIPMENT IS NEEDED FOR A DISTILLERY?
One of the first questions people often ask us is, “How big of a still should I get?” While this is an important question, you need to have answers to many other questions first, because the equipment you need for your distillery depends, first and foremost, on your vision for your distillery. You need to begin by defining what products you want to produce, at what volume, and for what markets – and you do this first by creating a financial model and supporting strategic plan. With this information in place, you’re poised to get your ideal system designed so that it not only meets your needs to get started, but can grow and be adjusted down the road.
DESIGNING AN IDEAL DISTILLING SYSTEM
Most people think of a distillery and picture only the main distillation equipment for milling, cooking, fermenting, and distilling. But, there’s more to it than that. You’ll need support utility systems in place that make all of the well-known parts run – and run well.
In addition to determining the types of equipment you need, you’ll also want to design with flexibility in mind so you’ll be well-positioned to grow and able to produce all the products you want to offer. This especially comes into play when you’re considering the size of your distillery space, the layout of your equipment, and the capacity of your various types of equipment.
QUESTIONS TO CONSIDER IN DISTILLERY PLANNING
There are a multitude of questions to think through when planning your distillery, but below are just a few that hit on things we’ve seen industry folks overlook or make assumptions on in the past.
WHAT SPIRITS DO YOU WANT TO MAKE?
Different spirits need different equipment. For example, whiskey may be distilled with a simple pot still and just a few trays, whereas vodka typically needs multiple columns with closer to 40 trays in each to get it as pure as possible. And unless you want to spend a significant amount of time on an extensive washout procedure, you’ll likely want a completely separate still for your gin, too, so the botanical extracts don’t contaminate the batches of your other spirits.
WHAT ARE THE BUSINESS VOLUMES YOU NEED TO HIT?
You have to know what your business volumes are going to look like now, and in 5 years, to do calculations based on the output needed to support those volumes and what size vessels can deliver those outputs. At Thoroughbred, our distillery engineers strategically size everything to comfortably hit the right output amounts on a single work shift. This is an important factor for expediency and convenience, but especially to keep your labor costs down. If you don’t already know, you’ll quickly learn, labor is a major cost driver for a distillery.
HOW LONG DOES IT TAKE TO GET EQUIPMENT?
Distillation equipment usually has the longest lead time in terms of the types of equipment you’ll be ordering. Metal fabricating companies, like Vendome, are doing your tanks, stills, etc., and with them, it’s typically 8-12 months to completion from the time you place the order. With other lesser-known vendors, it can take 6-8 months, but you want to be careful that you’re working with a trustworthy and proven manufacturer. For your support utility systems, such as boilers and compressors, the wait times are typically about 3-4 months. However, recent demand has created backlogs for these items as well. Pro tip: We usually advocate for going with someone with a good local presence for your support utility systems so someone in your area can come service it right away when needed.
Getting these pieces right and making sure they align with your financial and business strategy are critical to avoiding costly mistakes and being prepared for a bright future. At Thoroughbred, we use our collective experience and expertise to create accurate business models with the products and volumes you want to make so, together, we can build a successful distillery.